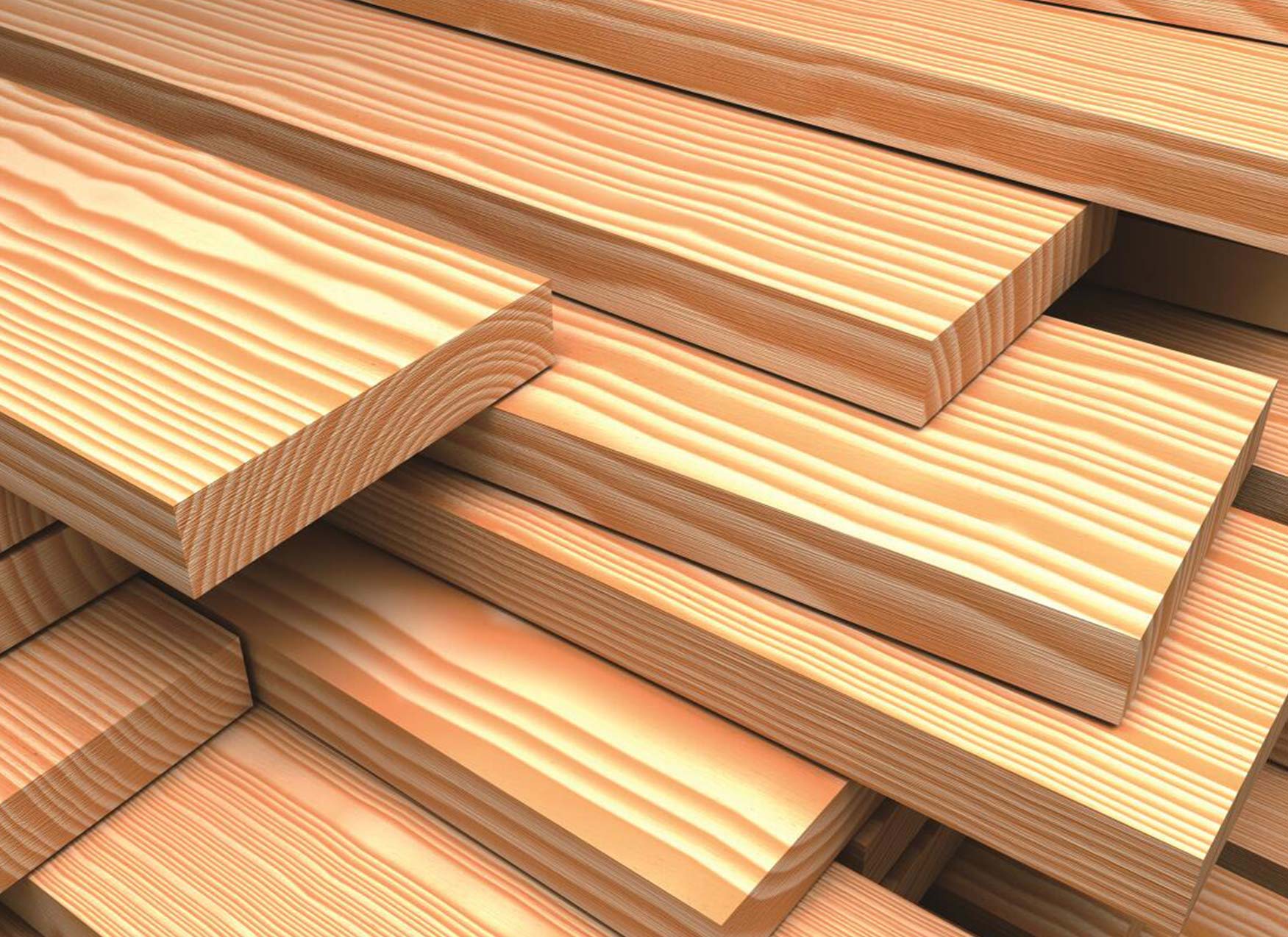
Facts about Fire Retardant Treated Wood
There are many first-rate wood species to choose from for new builds and renovations. Wood is a tried and true material to use in classic and modern construction. While the choice is important as to which material to use, and possibly which kind of stain to have applied, there is an additional treatment to consider after the wood selection is made, and that is whether or not to have a fire retardant treatment applied to the wood.
According to the National Building Code of Canada, “Fire-retardant-treated wood” (FRTW) is imbued with fire-retardant chemicals in solution under high pressure in accordance with the CAN/CSA-080 Series of Standards, Wood Preservation. Therefore, the treatment in this respect decreases surface burning characteristics, like flame spread, rate of fuel, and smoke impact. Certainly, any builder can understand the importance of having this treatment applied to their project, particularly for a new school.

According to owner Brian Jenkins at Longhouse Specialty Forest Products, his company has been applying various non-toxic lumber fire retardant treatments since 1999. Furthermore, the treatment may be applied to all lumber species, such as Douglas fir or Western Red Cedar. As to the costs, they are similar to pre-staining rates.
The procedure must be applied before other stains to dry, untreated lumber. So, if required by an architect, a builder would purchase the Fire Spread Rating (FSR) treatment to fulfill their specifications. The treatment is water-based, non-toxic soluble chemicals suspended using water as a medium to apply to the lumber. Next, the wood is dried, with pre-staining applied later. The fire retardant can be used for interior or exterior applications, such as lumber siding on the exterior or fir timbers on the interior.

To illustrate, Western Red and Yellow Cedar lumber of 19 mm thickness have a FSR of 73 and 78, respectively. Preventative fire treatment is employed by Longhouse to protect your lumber investment to Canadian standard CAN ULC S-102 < 25 FSR and American standard “CLASS A” < 25 FSR, as stated in the company brochure.
The professionals at Longhouse have applied this treatment for all types of building developments throughout British Columbia. Projects range from schools, institutions, hotels, commercial buildings, to both single and multi-residential builds.
For further information, contact the knowledgeable staff at their Parksville office. They are filled with valuable information and two decades of experience in the application process.